Vehicle - System Understanding
Driving Dynamics, Driving Comfort and Tires
In the research area of vehicle dynamics, ride comfort and tires, particular importance is attached to the experimental and virtual identification and simulation of vehicle dynamics and comfort-relevant overall vehicle, subsystem and component characteristics. For more than 20 years, long-term research and development cooperations have existed with various automotive, system and component manufacturers as well as industrial service providers and software developers. One of the key points is, for example, to describe and understand the tire under all boundary conditions in real driving operation and road contact as well as with the existing interactions with subsystems in the overall vehicle context and to map them with novel simulation approaches. The existing and emerging complex understanding of the physical chain of effects with the associated new approaches to resolving conflicting goals will enable, for example, demand-oriented concept development, an increase in efficiency in the development and validation process, and the use of innovative development methods.
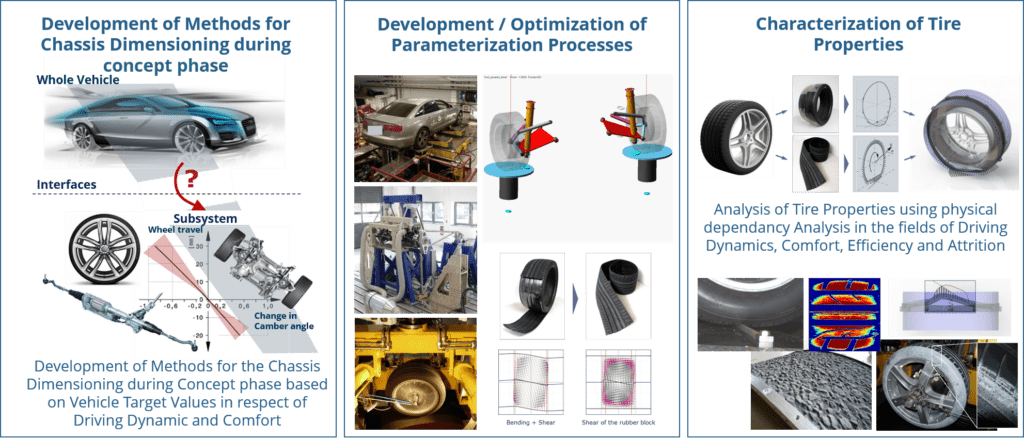
Testing:
- Complete vehicle investigations and model parameterizations for Kinematics and Compliance (K&C) – static and dynamic
- Vibration and transmission behavior up to 30 Hz (ride comfort and driving dynamics)
- Determination of replacement spring rate and friction analyses on the complete vehicle or on vehicle axles
- Determination of the dynamic transmission behavior of components and vehicle axles
- Wide range of property analyses on tires, shock absorbers, brakes, axles, steering and complete vehicle
- Benchmarking and load data determination
Simulation:
- Principle/concept models for vehicle dynamics and ride comfort including data and parameter identification
- Digital basic/preliminary system design and development of vehicle dynamics control systems
- Vehicle subsystem and component models of varying complexity
- Reliable and individual parameter identification and validation methods
Research/Development:
- Control strategies/control systems for basic design, for principle models and for chassis control system modeling/parameterization
- Active/intelligent chassis controller development – AI-based (deep learning) algorithms
- Objectification, basic design and virtualization of vehicle dynamics, ride comfort and steering feel
- Method development for parameter identification from complete vehicle to component level
- Functional models of comfort-relevant vibration phenomena
- Characterization and prediction of degraded landing gears / predictive maintenance
- Development methods and functional models in the field of leisure and special vehicles
- Alternative / interdisciplinary (model) approaches to data acquisition and (inventory) data processing
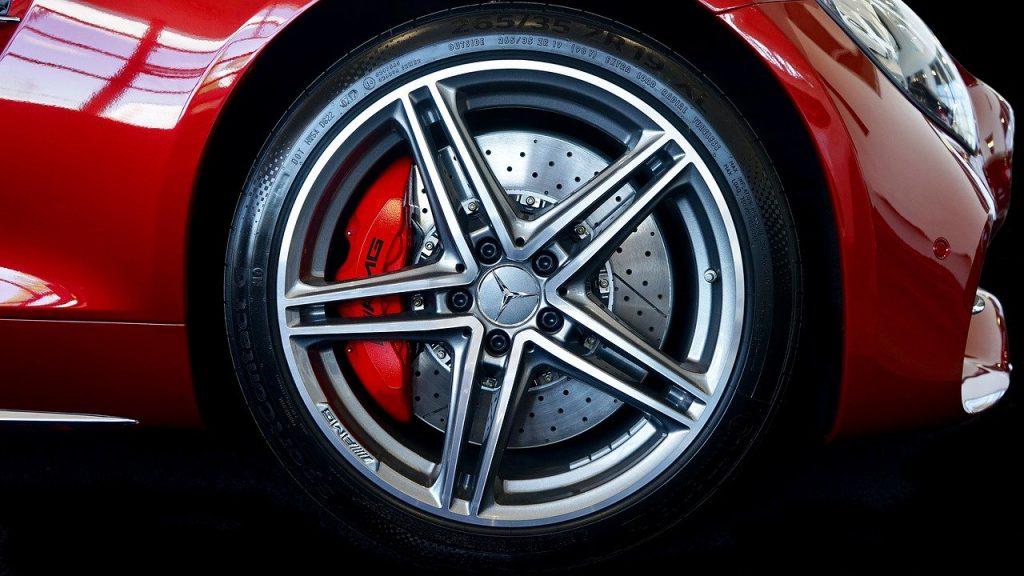
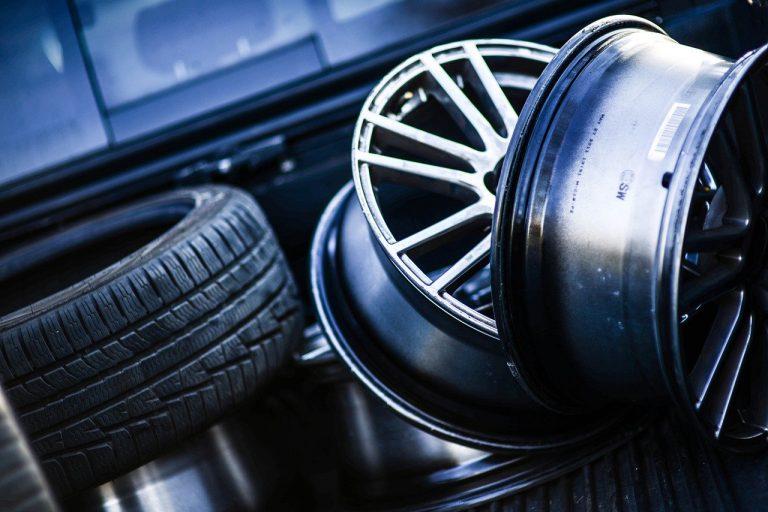
Tires and Wheels – Testing, Simulation, Method Development and Research
As a competent partner, we are available to you as a team for tire and wheel technologies to answer your questions and requirements regarding tire and wheel issues. Whether testing, simulation, method development or research projects; thanks to our extensive test rig infrastructure and simulation tools from component to complete vehicle level, we take a holistic, systemic view of the topic of tires and wheels.
From professional test preparation and organization to the metrological determination of all required data on our test rigs to comprehensive data analysis/evaluation, as well as, for example, the fitting of tire models, we provide you with the complete process chain in line with your requirements and secured.
Thanks to our considerable test bench infrastructure, we are able to offer a variety of maneuvers / measurement procedures / special requirements for the characterization of tires and/or wheel systems as well as for the parameterization of simulation models.
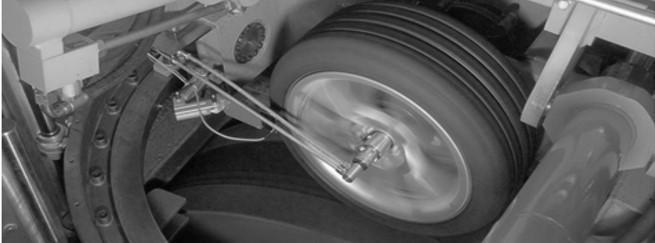
Testing:
- Forces & Moments, Footprint, 3D Outer Contour Scan, Tire Cut Creation
- Friction value analysis on different surfaces
- Degradation analyses / wear and temperature behavior
- Rolling resistance measurement, NVH & modal analyses, benchmark
- Tire/rim/wheel systems, misuse analyses and other customer-specific testing
Simulation:
- Total vehicle simulations
- Identification of tire model parameters
- Development of own model approaches for vehicle dynamics and comfort
Research and Method Development:
- Intelligent and adaptive tires
- Research to reduce tire wear
- Identification of physical phenomena at the component, subsystem, and overall vehicle level related to tire pressure loss and tire-induced structure-borne noise
- Wheel/tire in the tolerance chain Chassis
- Rolling resistance, friction coefficient estimation as well as further customer-specific research tasks
Operational Stability and Noise Vibration Harshness (NVH)
Connected Testing
The vehicle is one of the most technically complex mass products of all. Our team is working on new methods and tools for the design and validation of vehicle properties. In doing so, we have focused on the main areas of operational stability and higher dynamic vibrations.
From the scientific investigation of physical relationships in components to the complete vehicle, we develop basic design tools, simulation methods and test bench solutions that make vehicle development more efficient and precise.
We have distinctive expertise in the areas of:
- Virtualization and Objectification
- Vibration Engineering
- Elastomeric Bearings
- Drives
- Landing Gears
We also have special expertise in the design of modern test fields, test benches for the realization of networked methods from simulation and testing (HiL) and virtual testing.
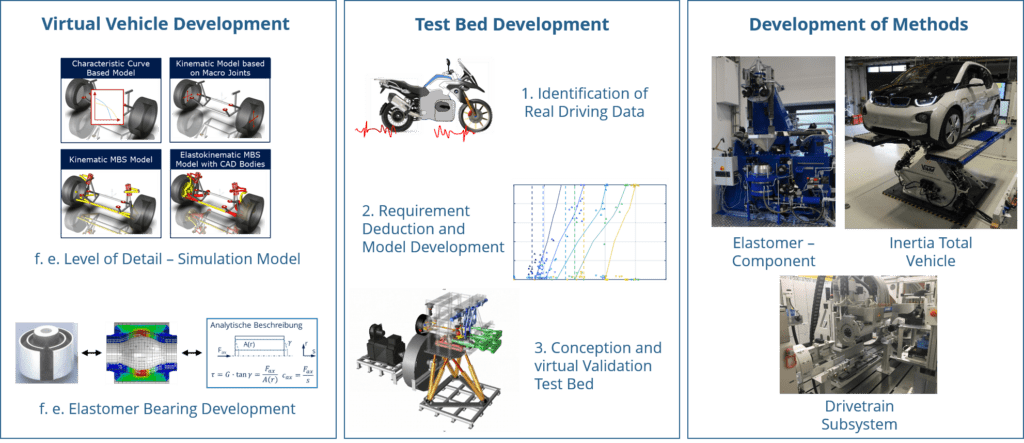
Testing:
- Measuring, checking and testing of:
– Drive Trains ( elec. / conv.)
– Vehicle Axles (elec. / conv.)
– Chassis Components
– Elastomeric Bearing
– Total Vehicles ( Cars / Motorcycles)
- Measuring, checking and testing of:
Simulation:
- Driving Maneuver Simulation MKS
- Parameter Identification
- Component and System Simulation MKS/FEM
- Parameter Identification
- DoE
Reasearch:
- Objectification Methods
- Test and Endurance Methods
- Networked Development Methods “Connected Testbeds”
- Elastomer Components
- DoE-based / virtual Protection
- Maneuver Reproduction / Road-to-Rig
- Quantification of Effects Chains on the Basis of Artificial Neural Networks